research topic(s): doubly curved glulam, doubly curved CLT, hyperbolic paraboloid shell, timber shells, robotic fabrication, bandsawn robotics
material: tree logs
size: 5" x 5" x 14' column + 5' x 5' x 3" CLT
principal investigator(s): Sasa Zivkovic of the Robotic Construction Lab (RCL) at Cornell
research team: Chi Zhang, Lauren Franco, Lawson Spencer
Henkel collaborators: Robert Payne, Daniel Current
funding provided by: Cornell Atkinson Center for Sustainability 2020 Academic Venture Fund (AFF) grant, David M. Einhorn Center for Community Engagement at Cornell University, 2022 AIA Upjohn Research Initiative grant
additional links: { pdf }
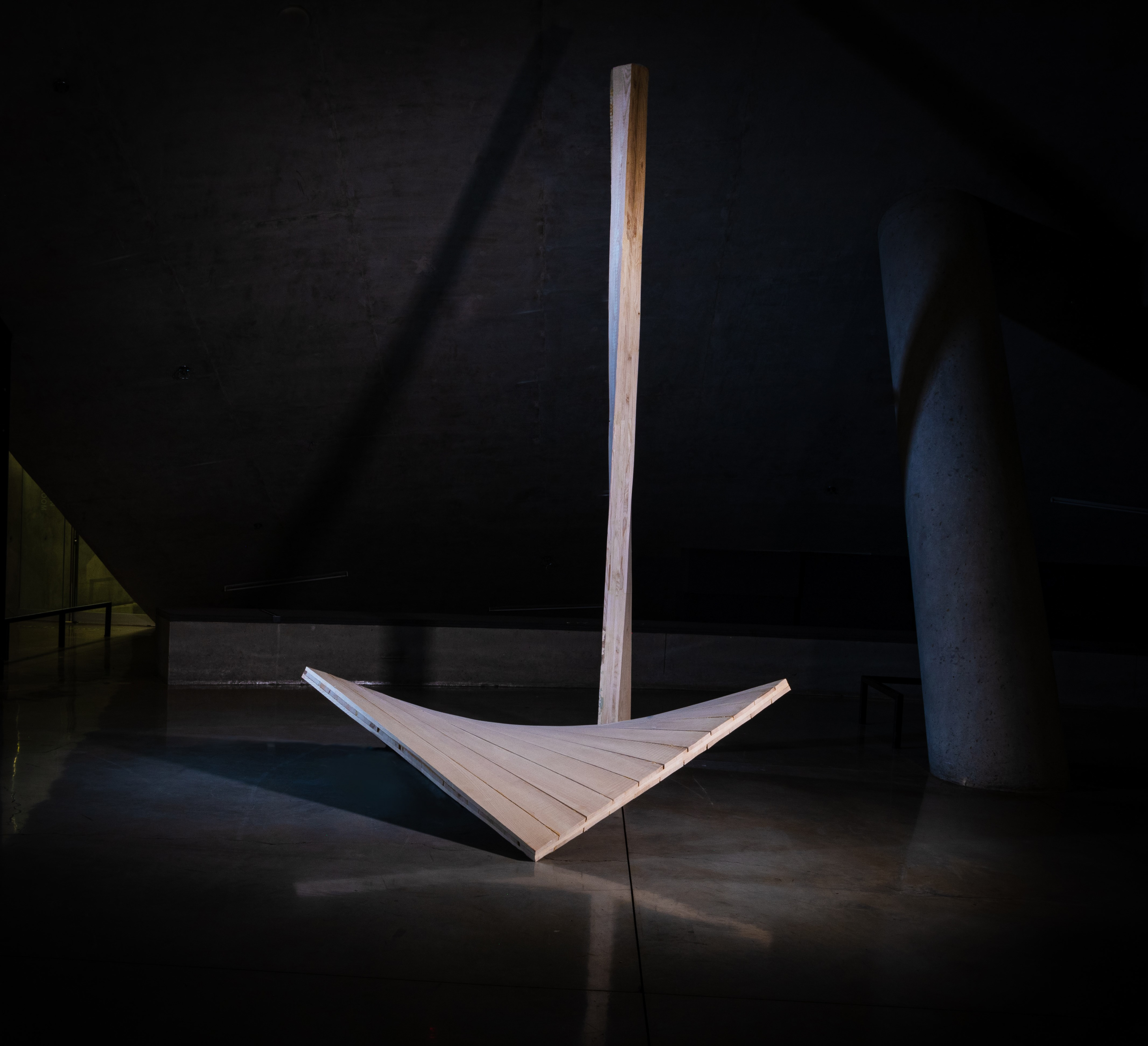
figure_01: photo of TwistedLam Column + CLT
summary:
As mass timber construction has become increasingly ubiquitous, doubly curved glued laminated timber (glulam) grid shell structures have challenged standard methods of glulam manufacturing which rely on a wasteful process of planing dimensional lumber into thin lamellas for lamination. The resulting glulam blanks are either milled or cut into doubly curved glulam blanks thereby discarding even more material. Instead of using dimensional lumber to manufacture doubly curved glulam and cross-laminated timber (CLT) blanks, Twistedlam is a robotic fabrication method that intervenes in the glulam and CLT manufacturing process at the raw material stage, to cut sets of doubly curved boards from a log with a bandsaw end effector on a 6-axis robotic arm. This method not only reduces the amount of discarded material but also simplifies the lamination of the process by eliminating the spring-back produced from twisting flat boards into doubly curved boards for the lamination of doubly curved glulam and CLT blanks. The viability and potential of this research are realized through two hyperbolic paraboloid prototypes: a doubly curved glulam column and a doubly curved CLT blank.
As mass timber construction has become increasingly ubiquitous, doubly curved glued laminated timber (glulam) grid shell structures have challenged standard methods of glulam manufacturing which rely on a wasteful process of planing dimensional lumber into thin lamellas for lamination. The resulting glulam blanks are either milled or cut into doubly curved glulam blanks thereby discarding even more material. Instead of using dimensional lumber to manufacture doubly curved glulam and cross-laminated timber (CLT) blanks, Twistedlam is a robotic fabrication method that intervenes in the glulam and CLT manufacturing process at the raw material stage, to cut sets of doubly curved boards from a log with a bandsaw end effector on a 6-axis robotic arm. This method not only reduces the amount of discarded material but also simplifies the lamination of the process by eliminating the spring-back produced from twisting flat boards into doubly curved boards for the lamination of doubly curved glulam and CLT blanks. The viability and potential of this research are realized through two hyperbolic paraboloid prototypes: a doubly curved glulam column and a doubly curved CLT blank.
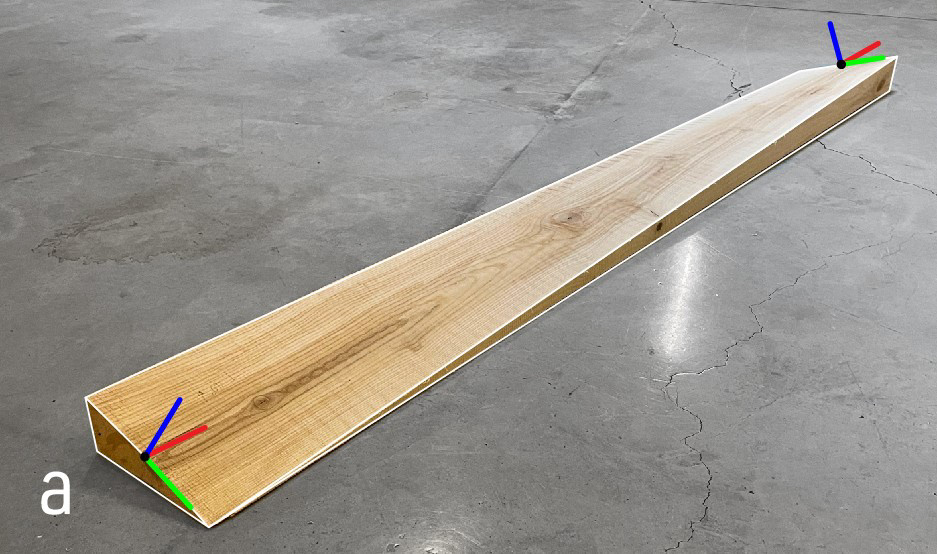
figure_02: twisted cut board
figure_03: video of 6-axis robotic arm with bandsaw end-effector making twisted cuts
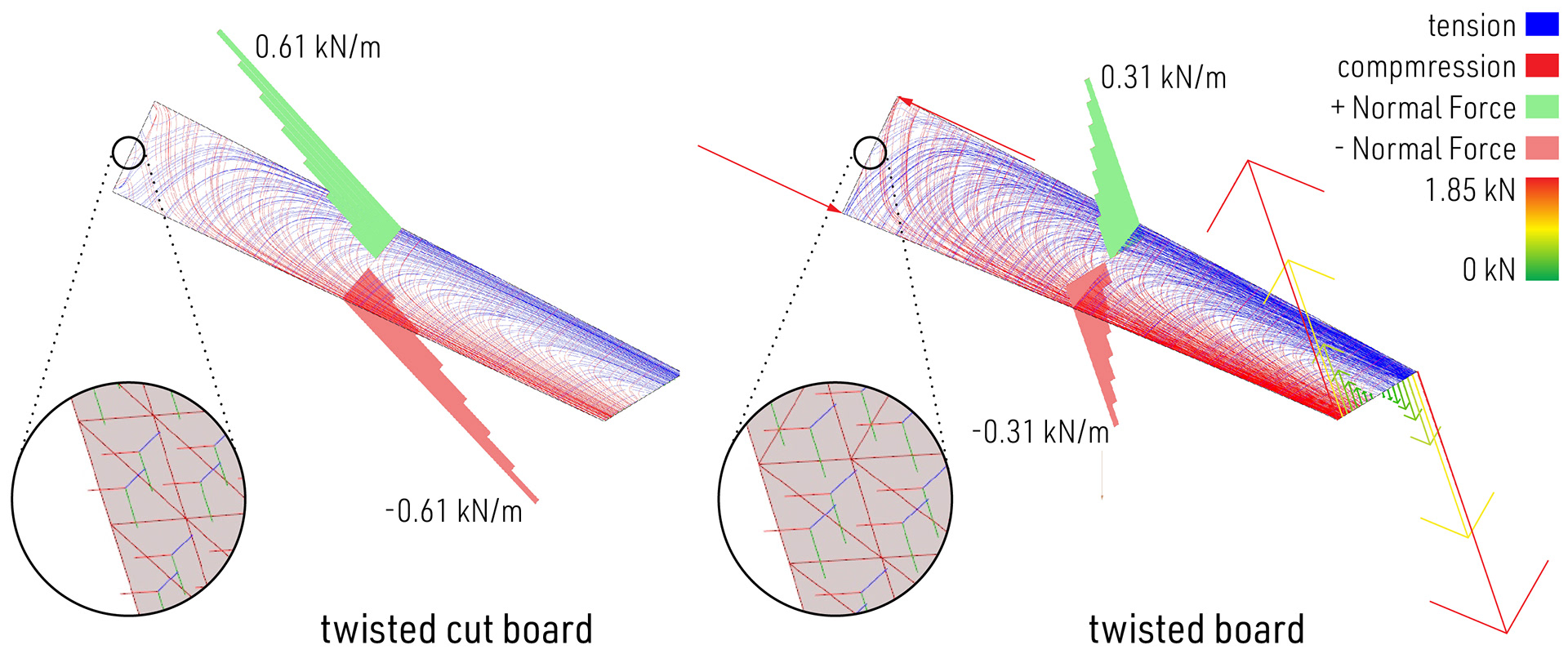
figure_04: structural implications of twisted cut boards and twisted boards
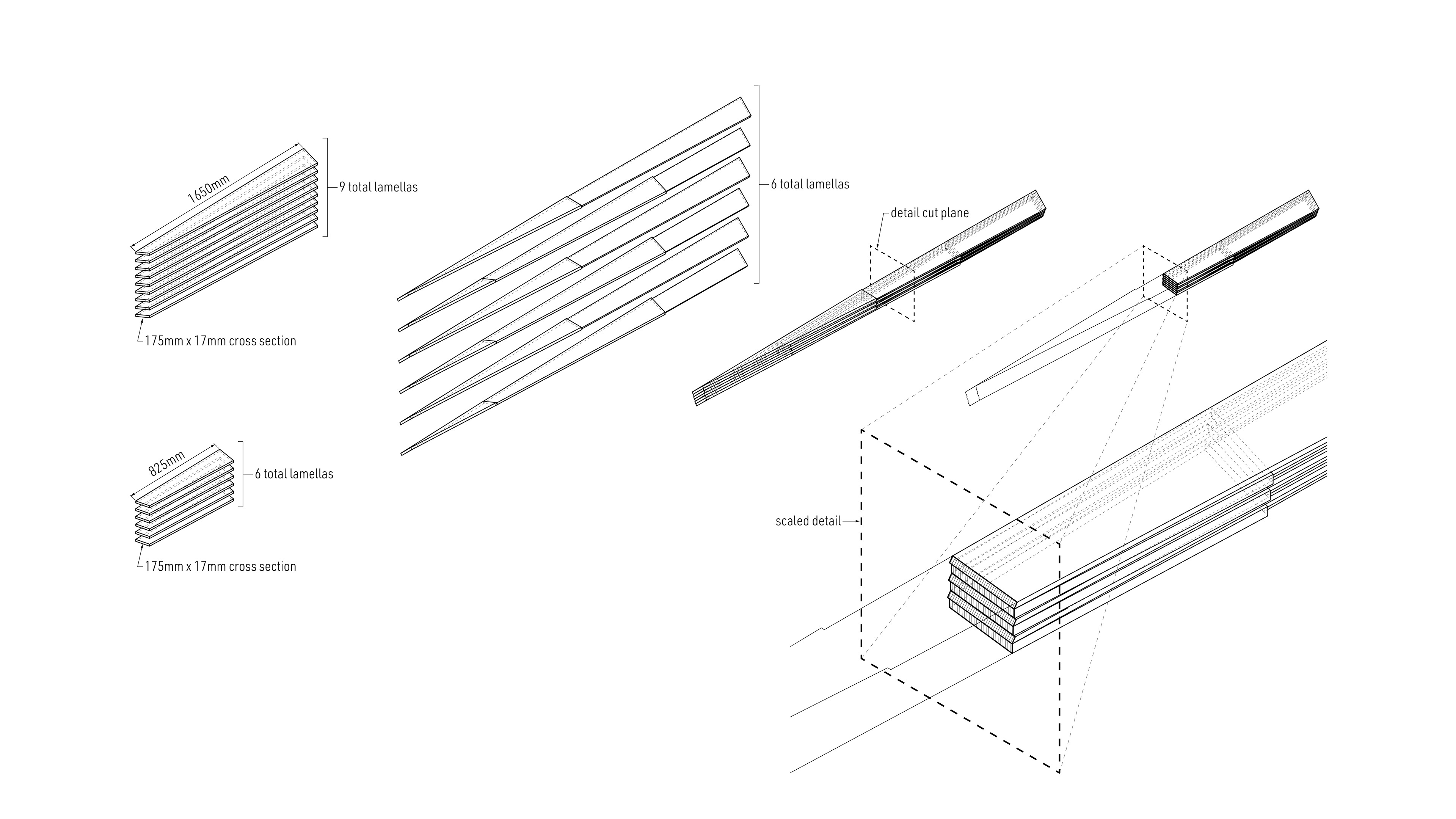
figure_05: column lay-up
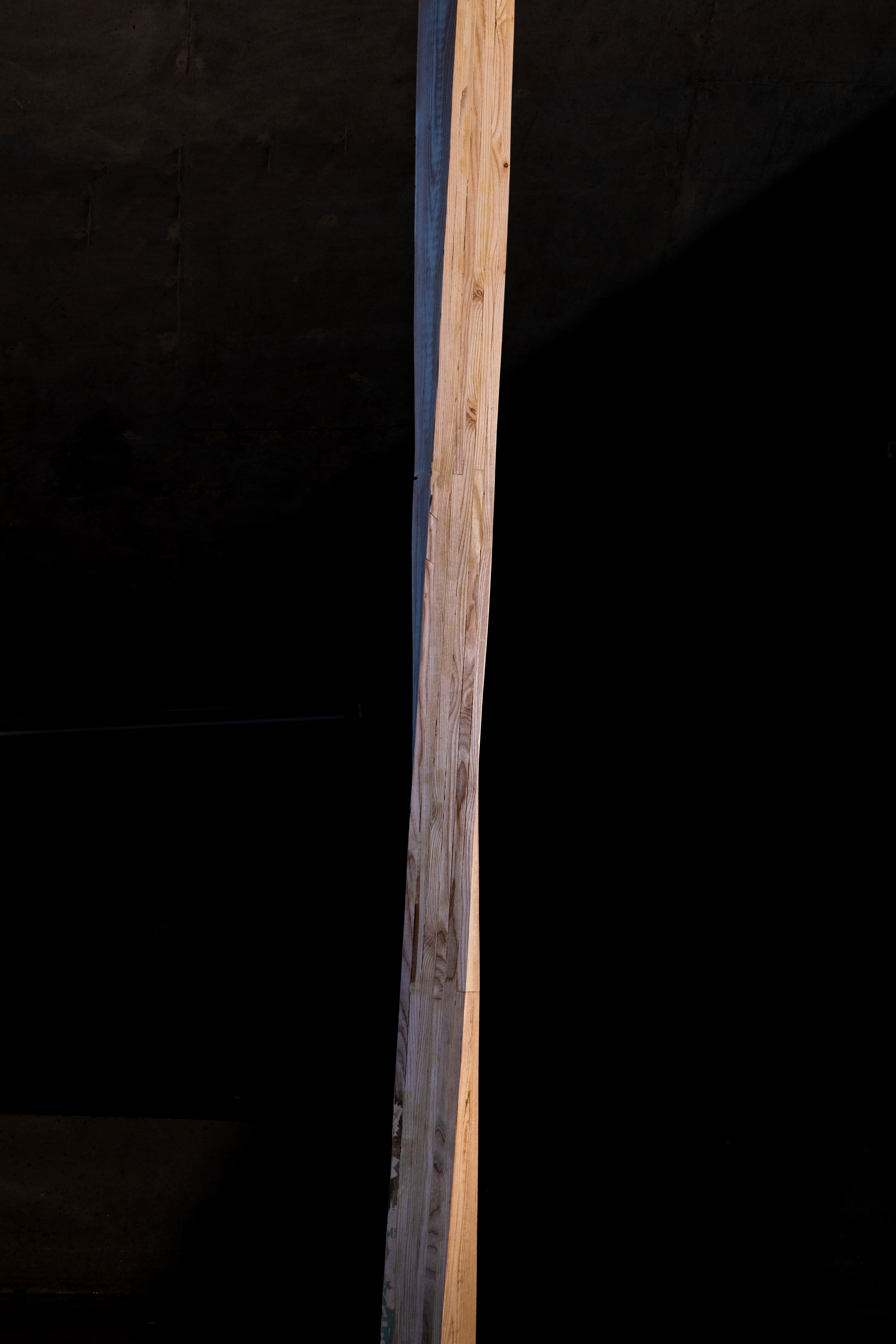
figure_06: detail photo of twisted column
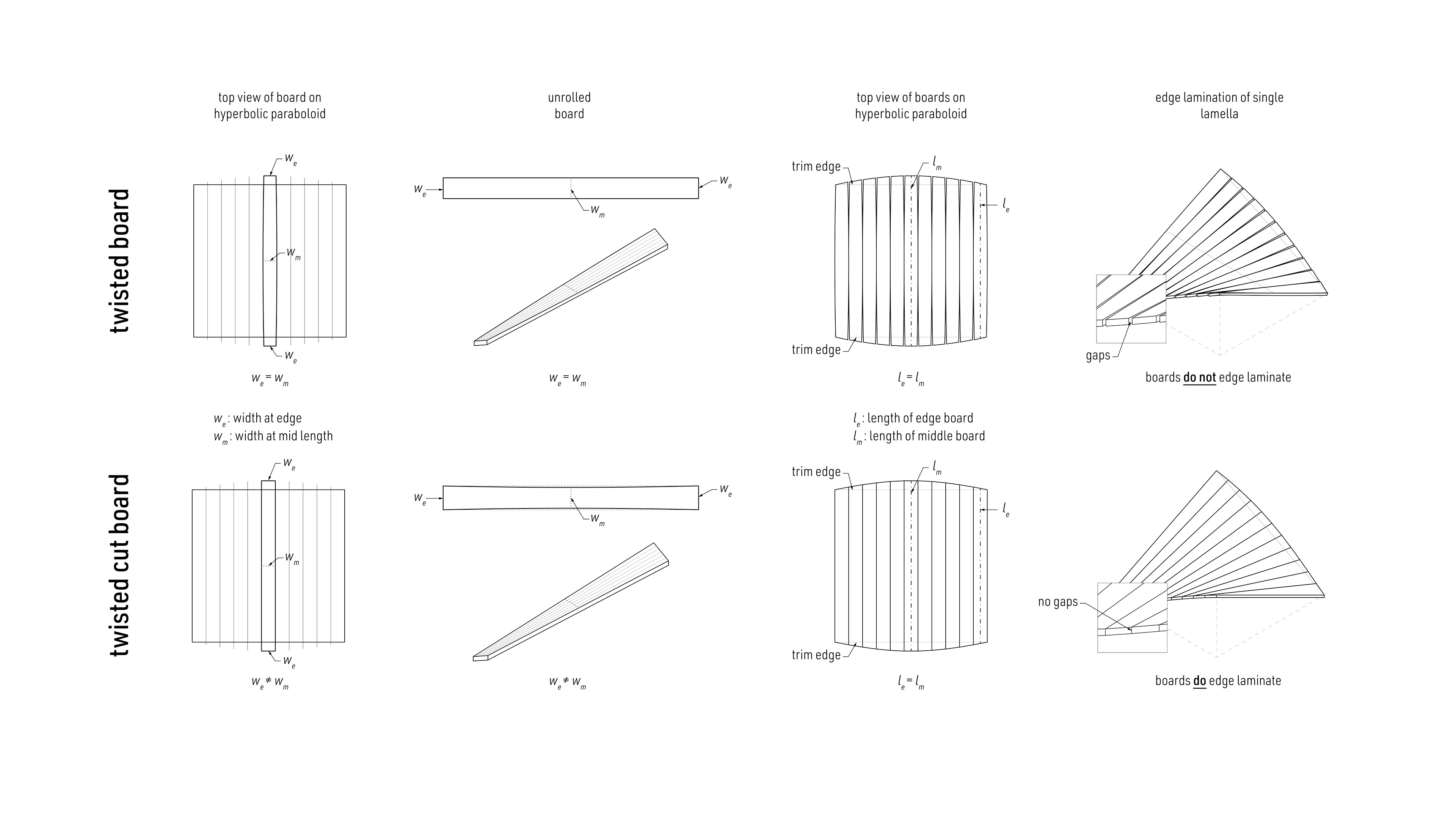
figure_08: effects of laminating twisted boards and twisted cut boards for cross-laminated timber (CLT)
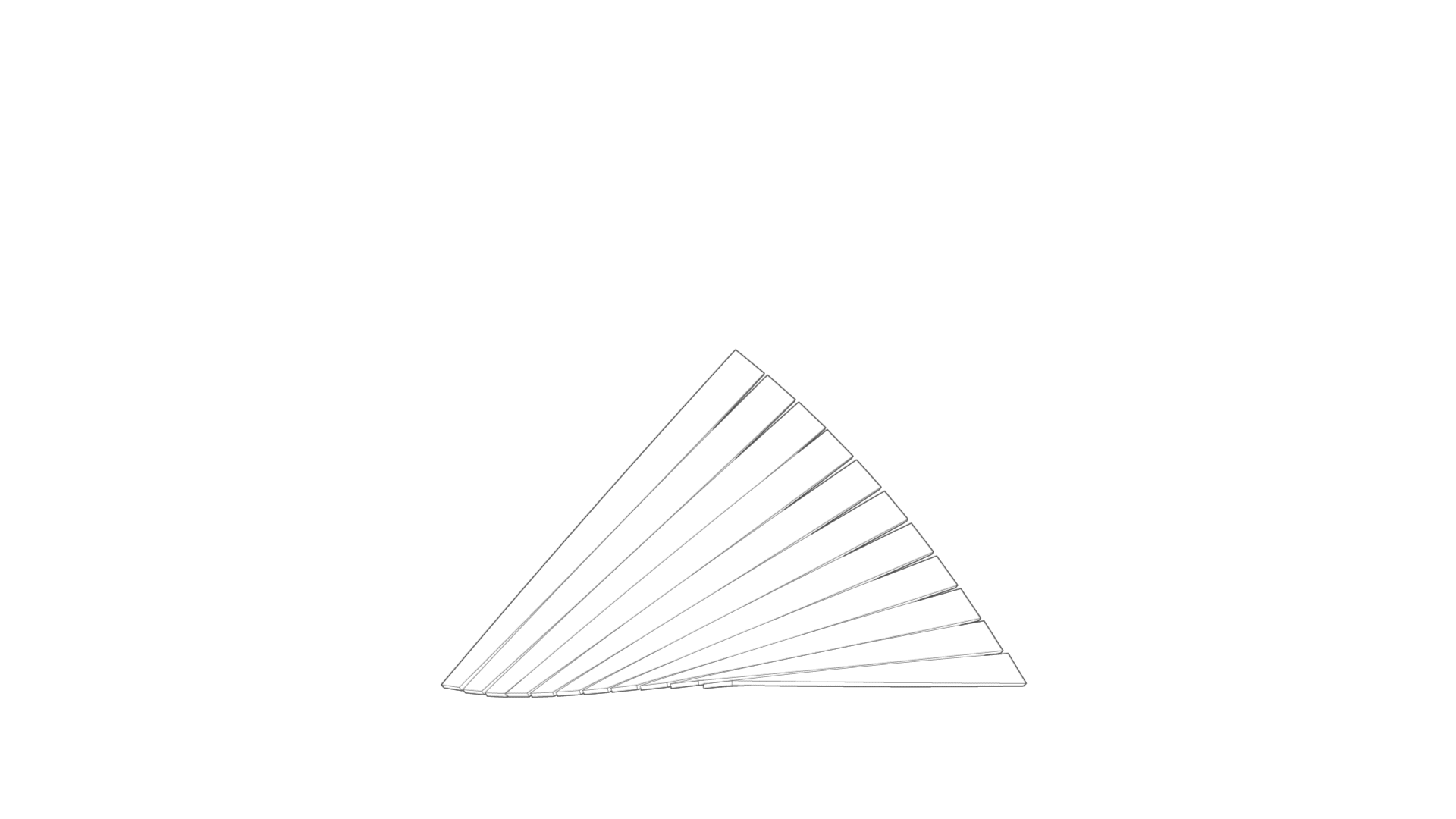
figure_09: animation of CLT lay-up with twisted boards
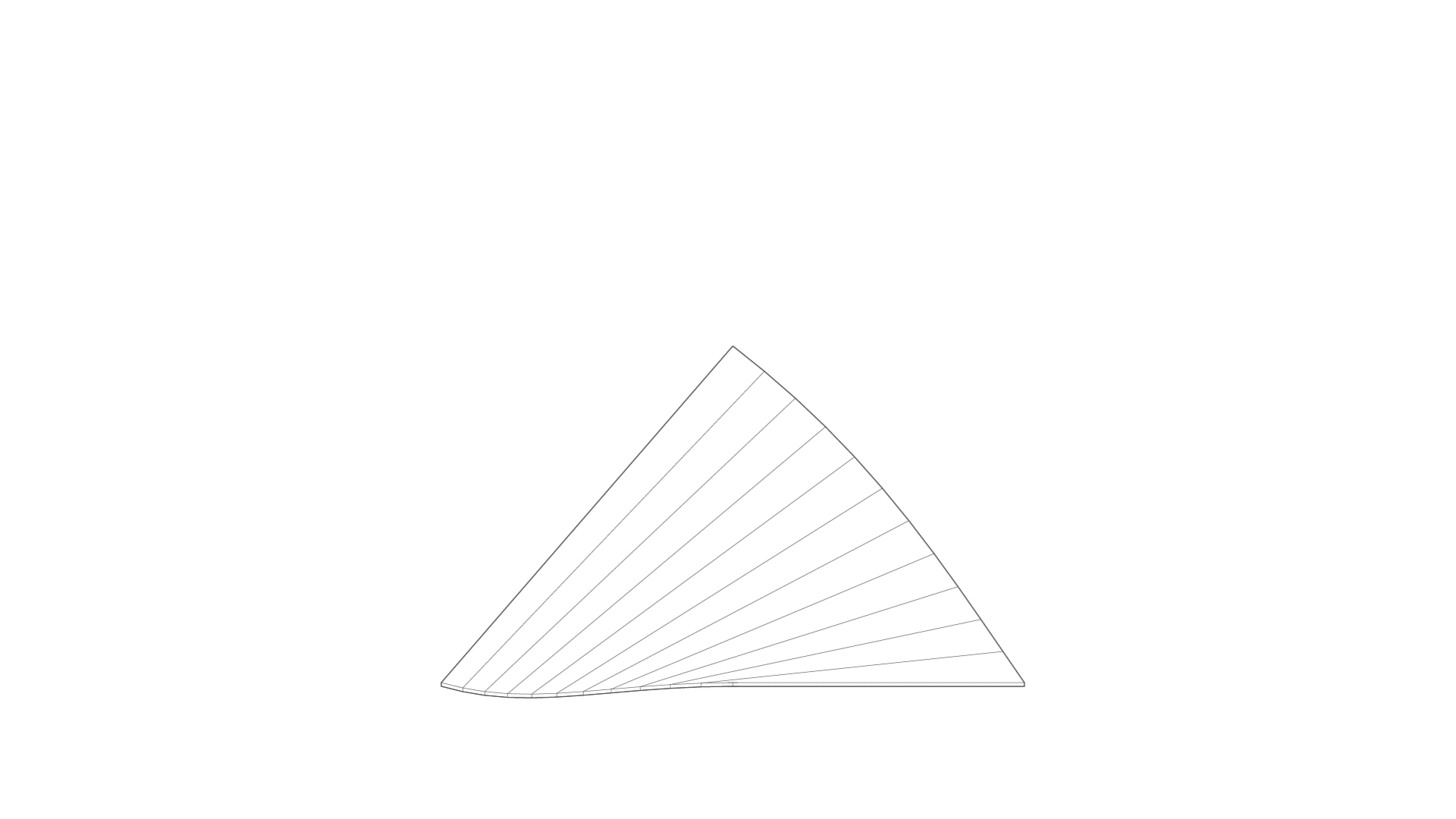
figure_10: animation of CLT lay-up with twisted cut boards
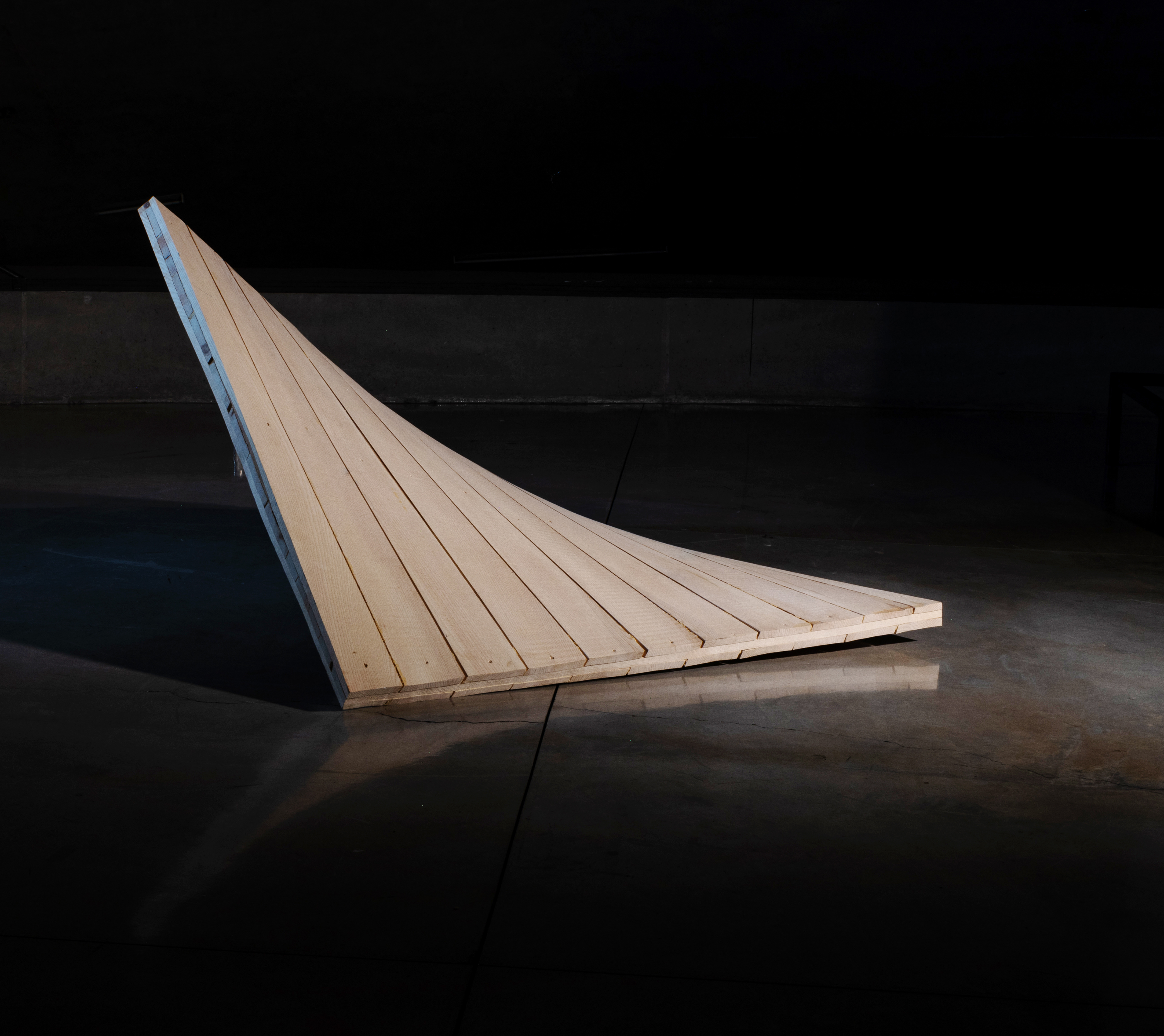
figure_11: hyperbolic paraboloid CLT with twisted cut boards