research topic(s): robotic fabrication, glulam optimization, timber finite element analysis
material: tree logs
size: 14' beams
principal investigator(s): Sasa Zivkovic, Director of the Robotic Construction Lab (RCL) at Cornell University
research team: Lawson Spencer, Yifei Peng, Peter Smallidge, Matthew T. Reiter
fabrication team: Chi Zhang, Lauren Franco, Shengkun Yang
Unalam collaborators: Craig Van Cott, Leif Van Cott, Rik Vndermeulen
Henkel collaborators : Robert Payne, Daniel Current
funding provided by: Cornell Atkinson Center for Sustainability 2020 Academic Venture Fund (AFF) grant, David M. Einhorn Center for Community Engagement at Cornell University, 2022 AIA Upjohn Research Initiative grant
peer-reviewed article: { pdf }
figure_01: Beam A perspective
Slimlam is a materially optimized manufacturing method to efficiently construct structurally optimized Glulam products through robotic fabrication. Using a bandsaw end effector on a 6-axis robotic arm, boards are programmed with varying thicknesses and assembled in a specific sequence to create beam shapes that taper to resist the loading effects. This approach reduces the total amount of material and weight in glulam beam products while maintaining a load capacity comparable to uniform glulam beams with a consistent rectangular cross-section made of dimensional lumber. While the method is not dependent on a particular wood species, the research utilizes ash wood, a locally available hardwood in North America due to the ongoing Emerald ash borer epidemic.
figure_02: cutting tapered boards
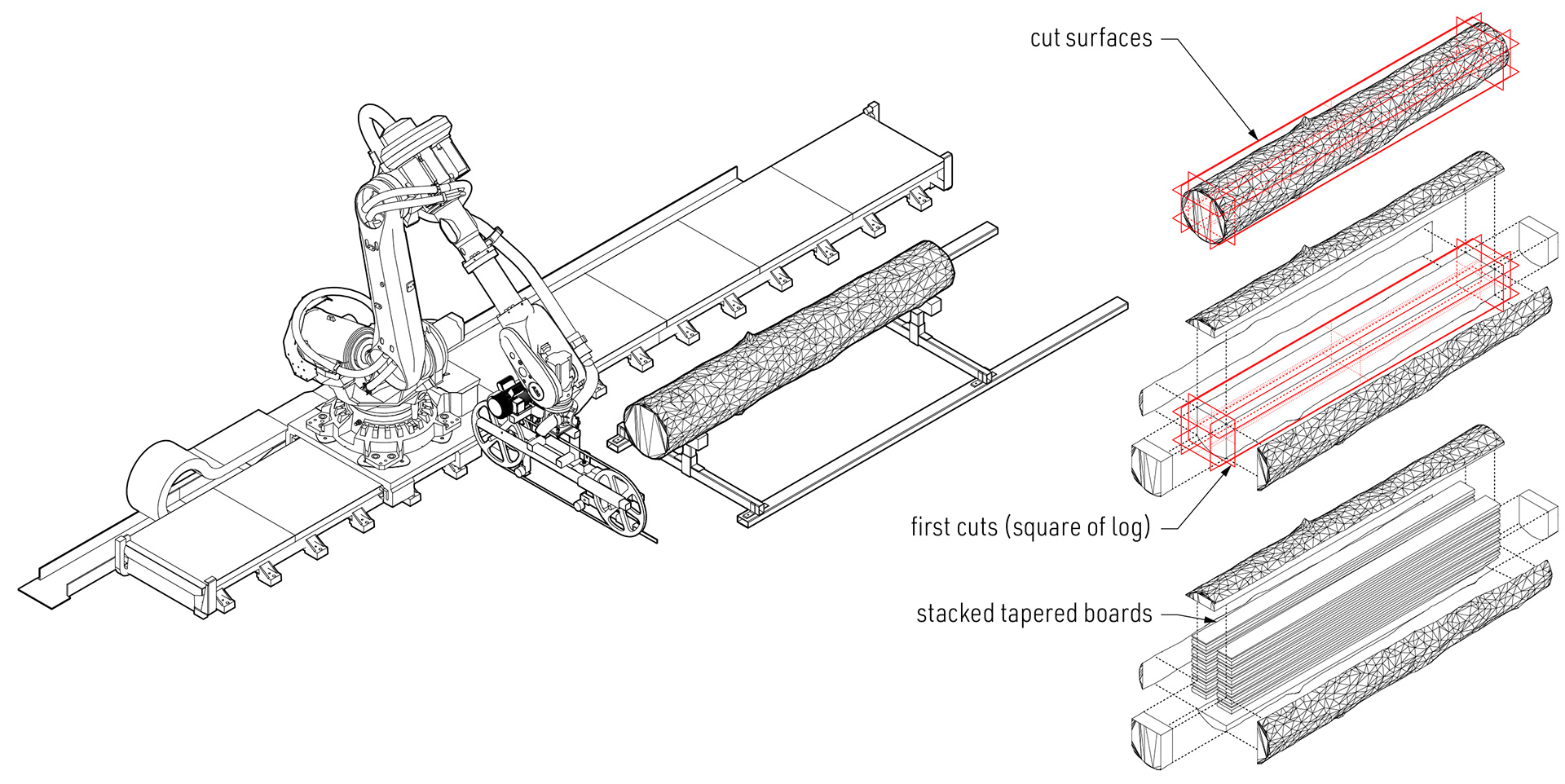
figure_03: squaring off workflow to cut tapered boards w/ 6-axis robotic arm and bandsaw end-effector
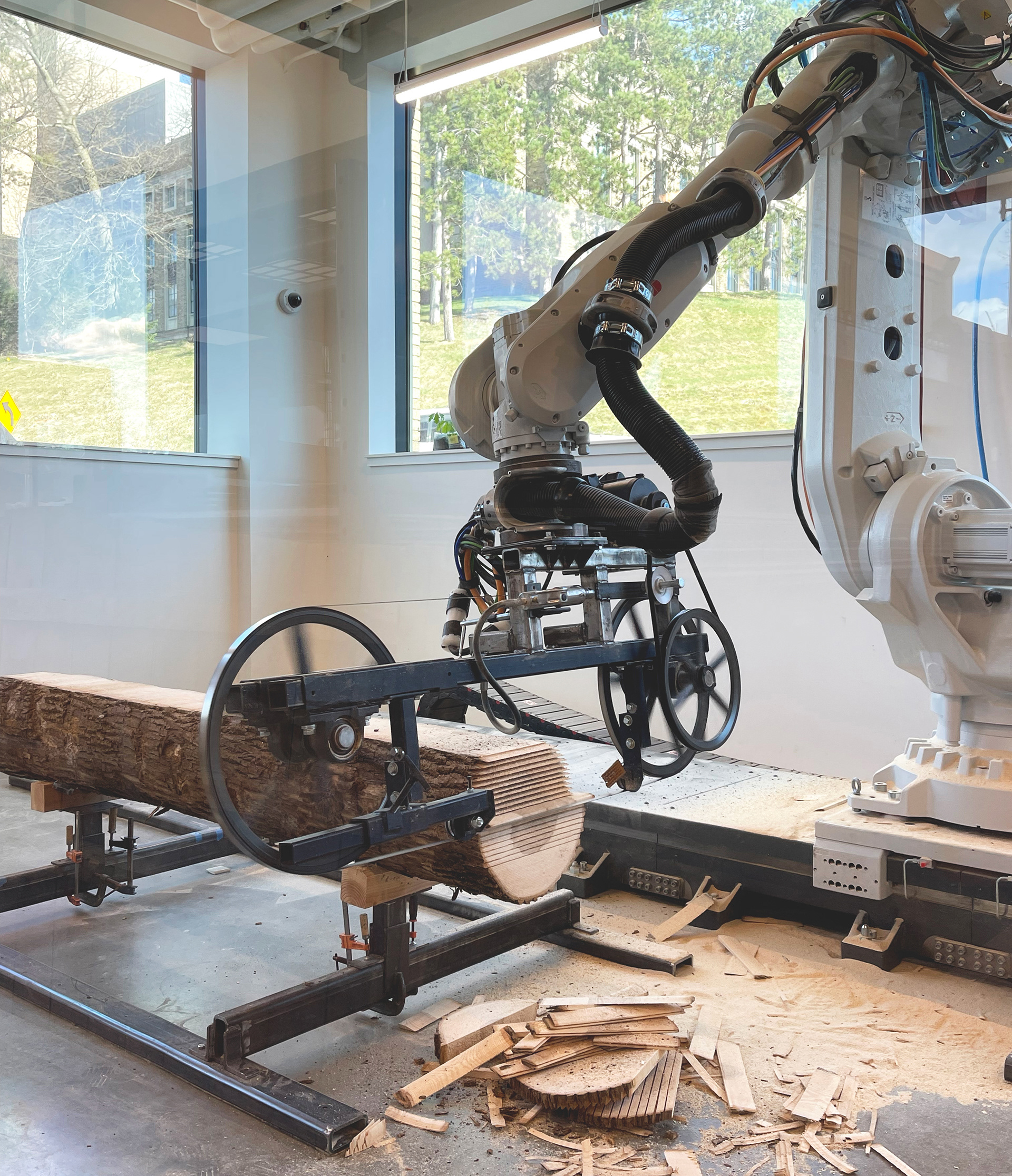
figure_04: cutting finger joints into log
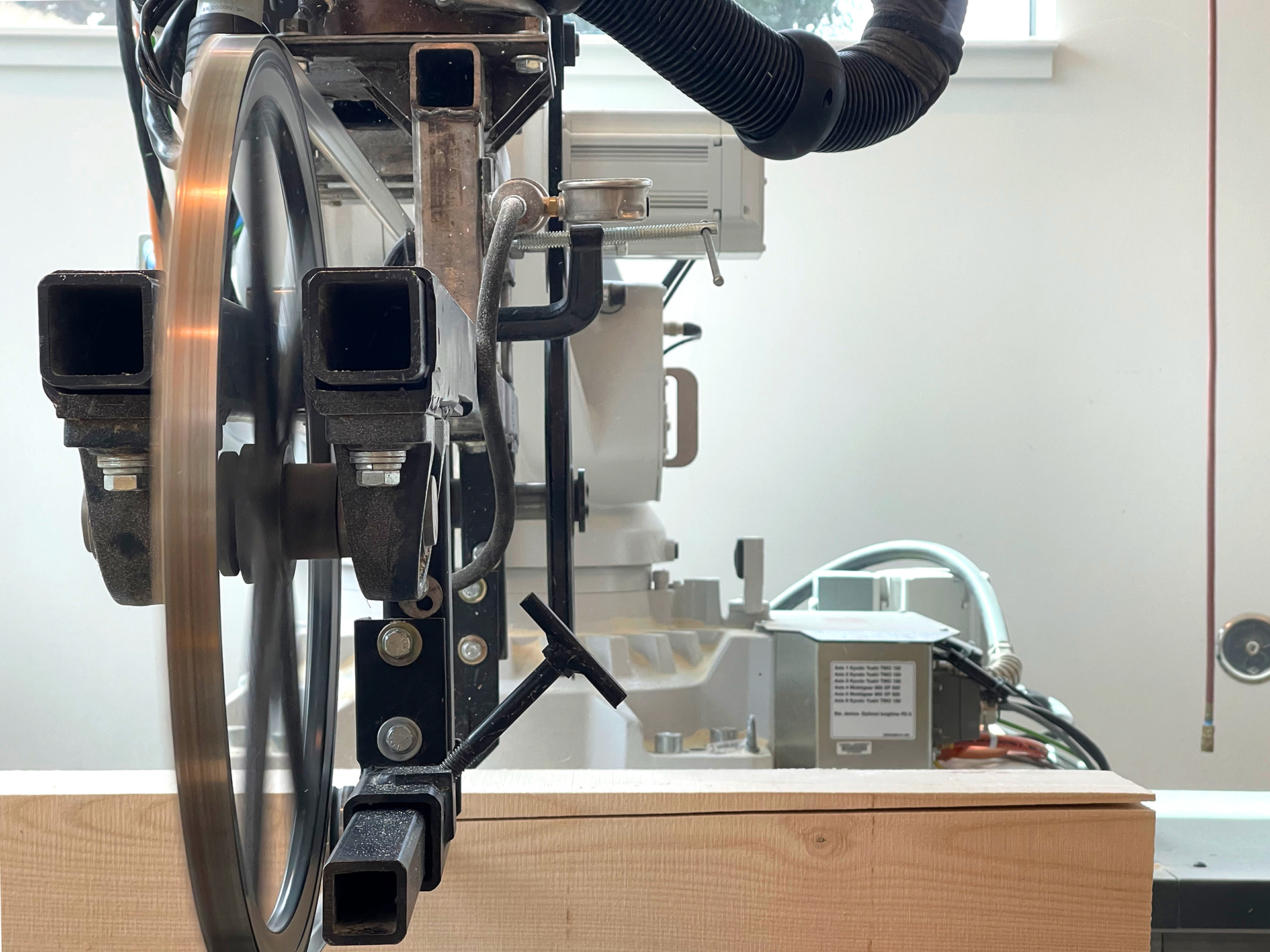
figure_05: robot cutting tapered boards
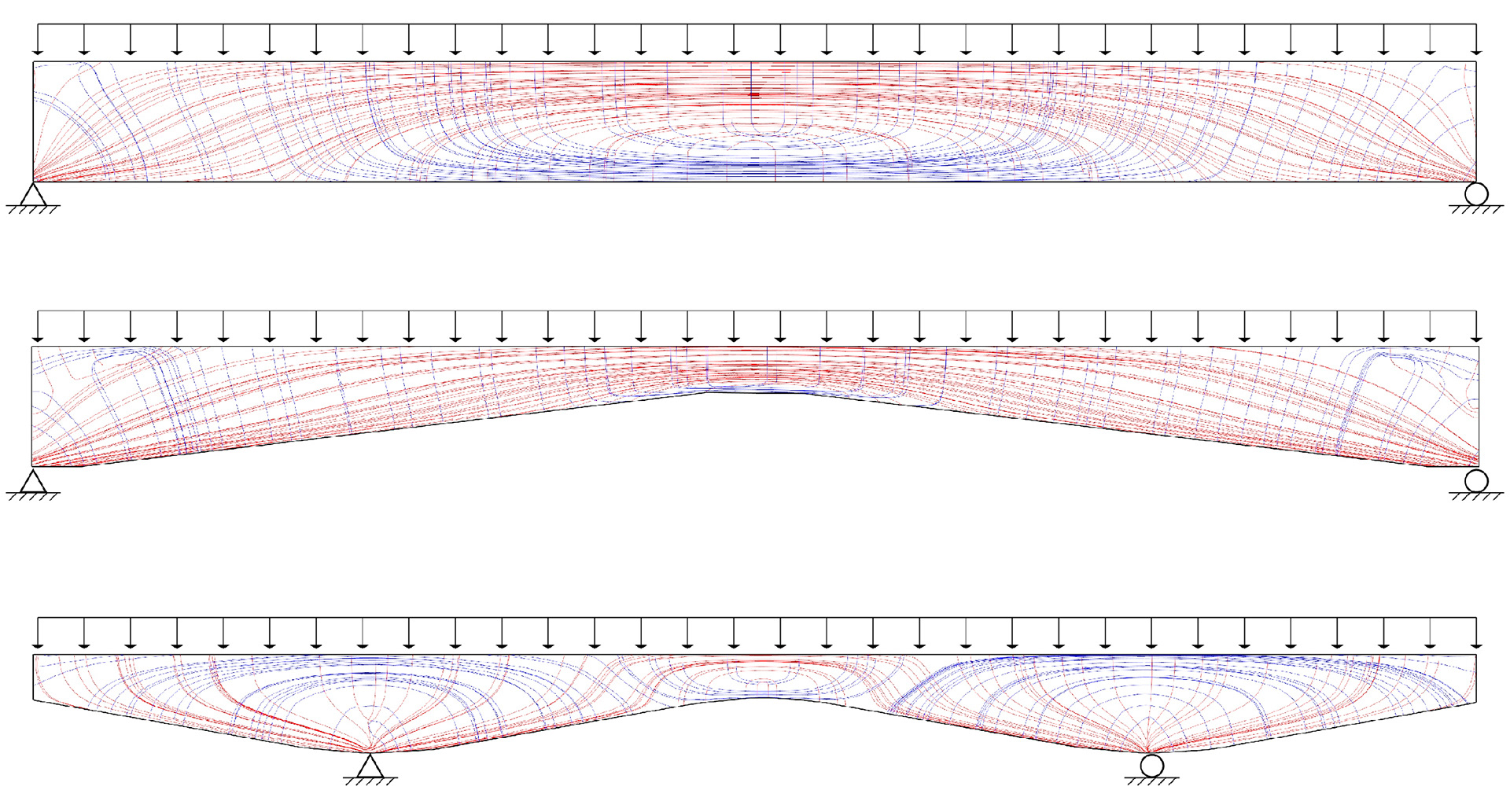
figure_06: compression (red) and tension (blue) force flows: from top to bottom - control beam, Beam A and Beam B.
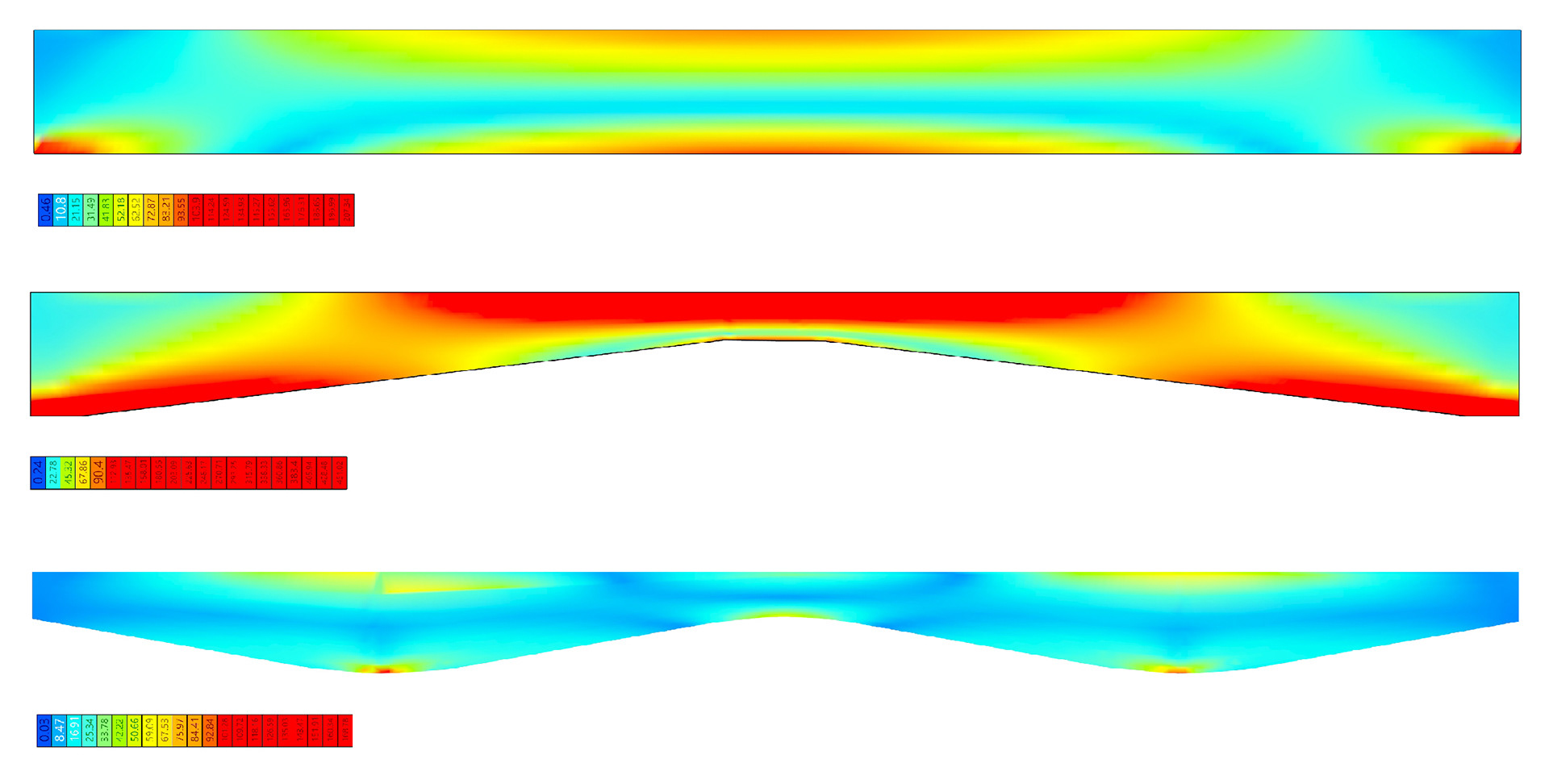
figure_07: utilization model: from top to bottom - control beam, Beam A and Beam B.
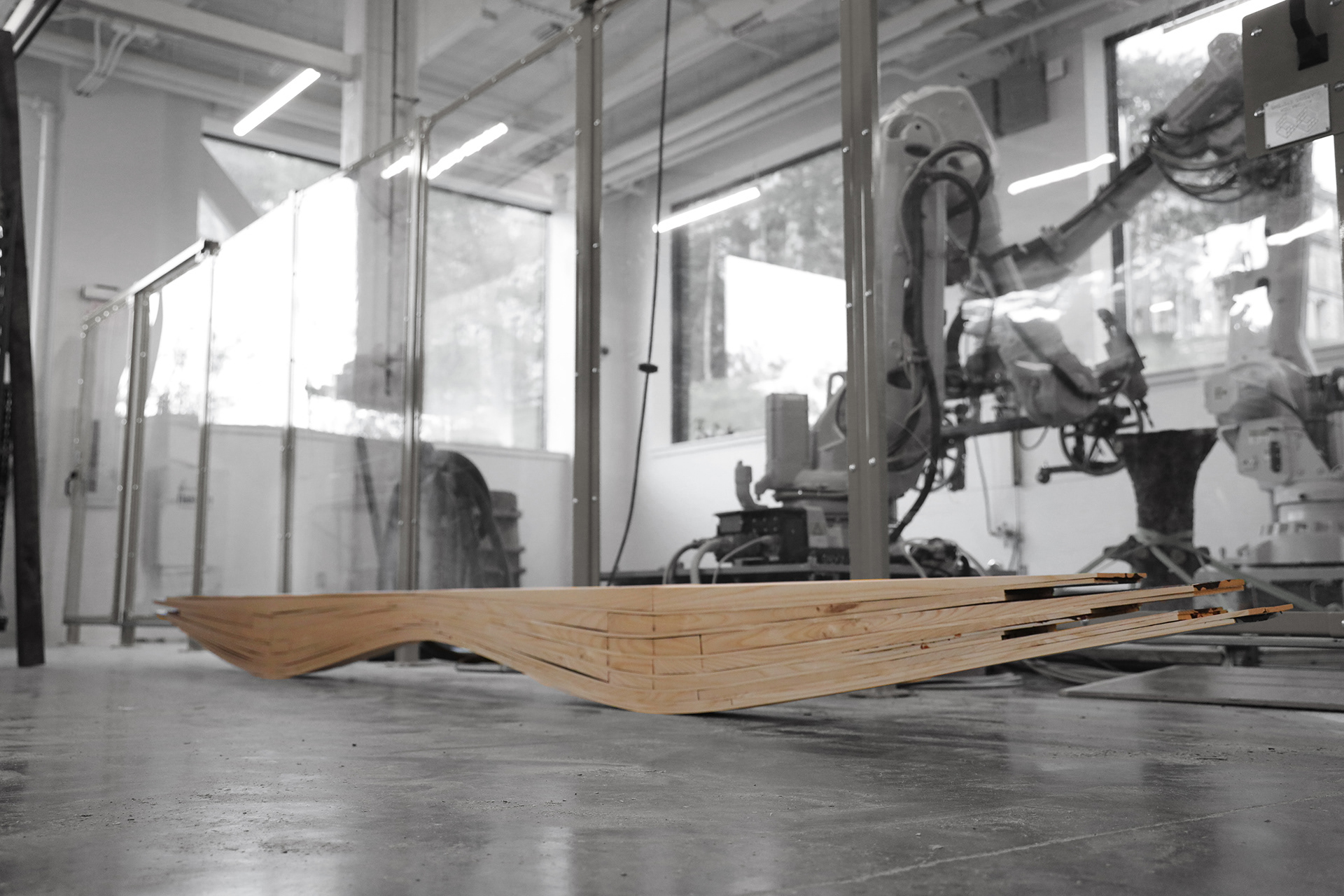
figure_08: Beam B perspective