research topic(s): 3D printed concrete (3DPC), gyroid structure, 3DPC gyroid, concrete additive manufacturing
material: 3D printed concrete (3DPC)
size: 500mm x 500mm x 500mm
principal investigator(s): Sasa Zivkovic of the Robotic Construction Lab (RCL) at Cornell and Sriramya Duddukuri Nair of Nair's Research Group
research team: Lawson Spencer, Moneeb Genedy, and James Strait
fabrication team: Dan Shen, Edie Blaze, Mark Krneta, Nikita Dolgopolov, Pulani Tremel, and John Conrad
funding provided by: Cornell Atkinson Center for Sustainability Academic Venture Fund and the College of Architecture, Art, and Planning at Cornell University
additional links: { link }
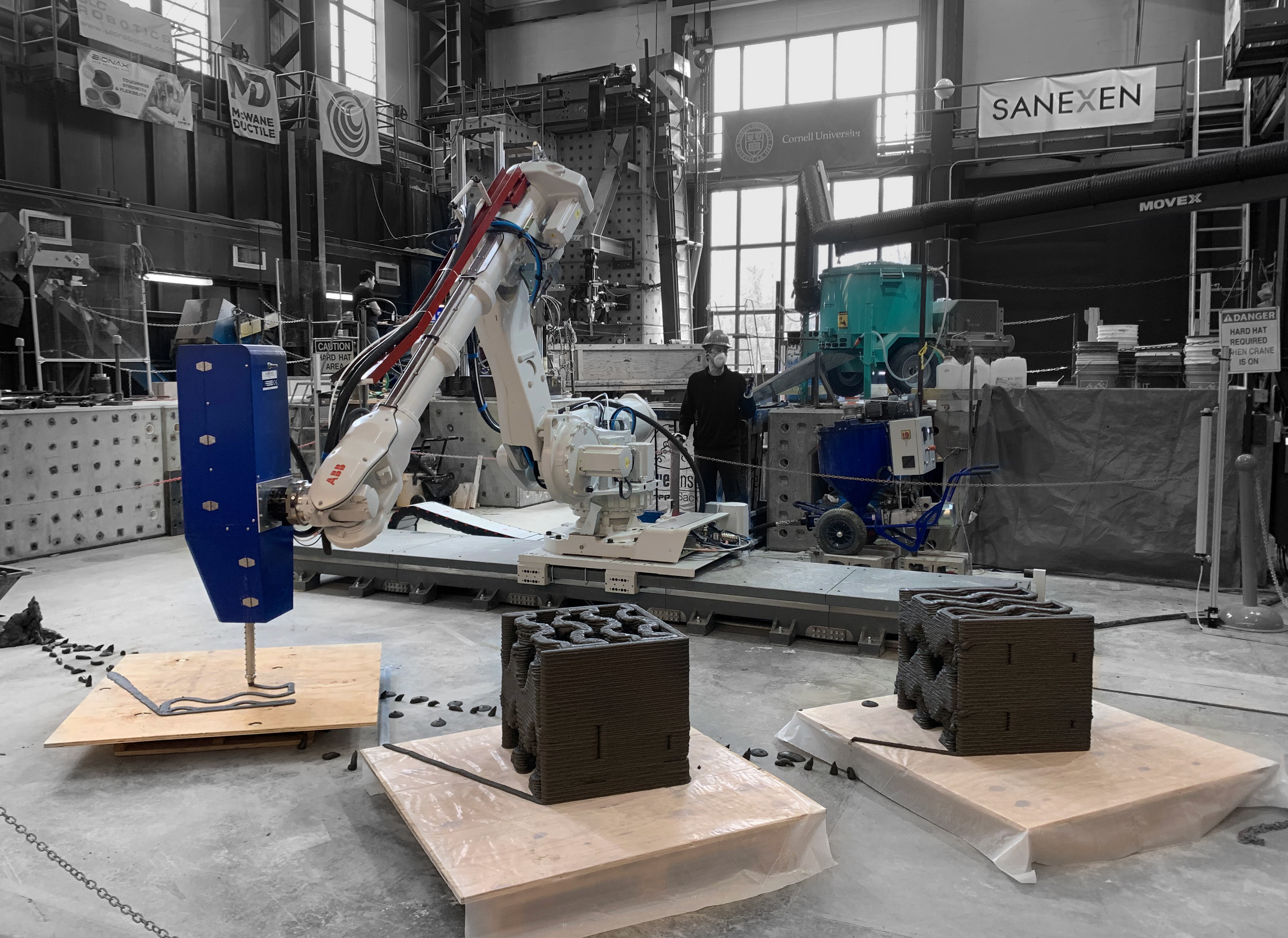
figure_01: 6-axis robotic arm extruding concrete with XtreeE end-effector
The gyroid is a triply periodic minimal surface (TPMS) that efficiently distributes stress under compressive loading in all Cartesian orientations. Despite the gyroid’s geometric ability to evenly distribute load, it has yet to be more broadly introduced to concrete additive manufacturing (AM) due to the difficulty of printing steep, doubly curved overhangs with a cementitious material. Consequently, the employment of the gyroid TPMS in AM has been limited to small and nano-scale applications. However, for doubly curved 3D printed concrete (3DPC) structures, the feasibility of the print is determined by the relationship between geometry, tool path design, and the mechanical and rheological properties of the concrete material being extruded. Using a 6-axis robotic arm with an accelerator-injection extruder as an end-effector, this research examines the fabrication limitations to construct a 3DPC gyroid.
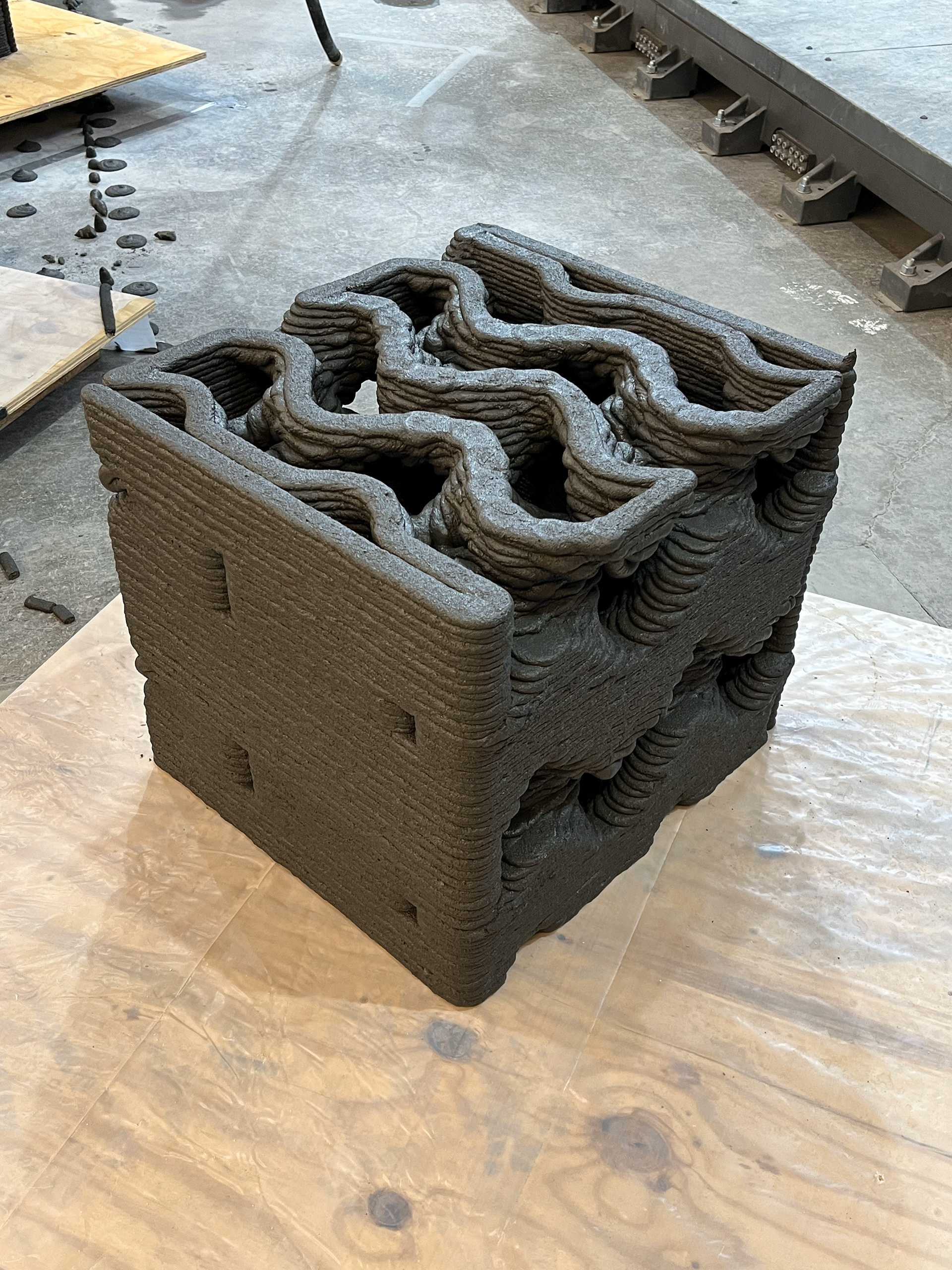
figure_02: cantilever test | John Conrad
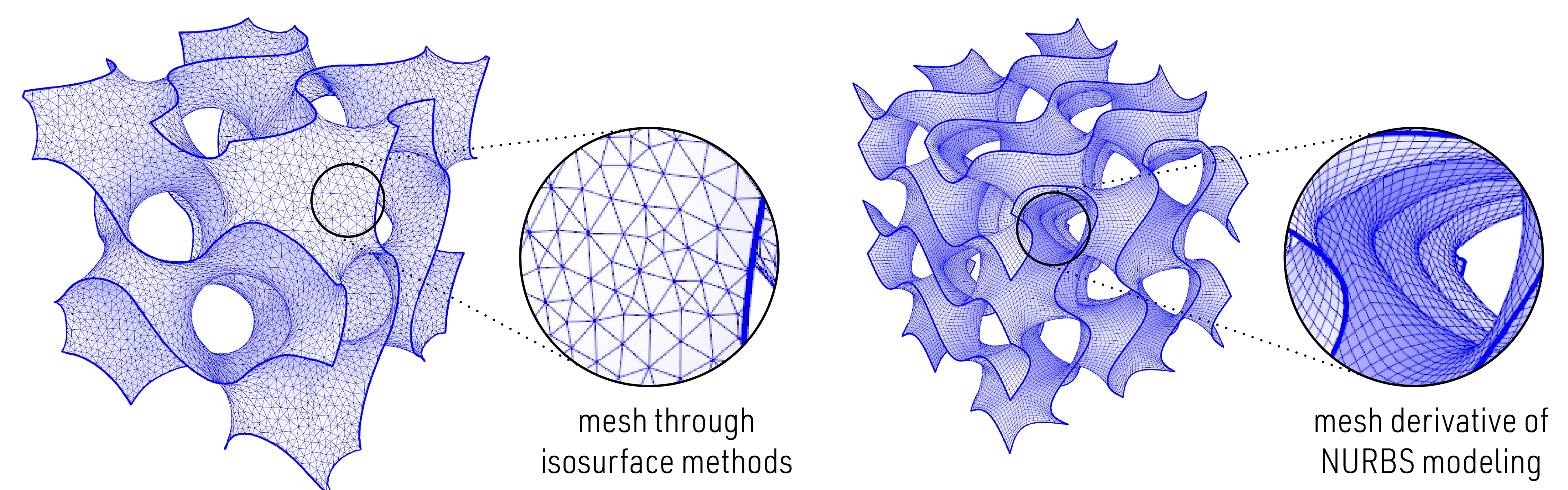
figure_03: isosurface modeling method vs. NURBS modeling method
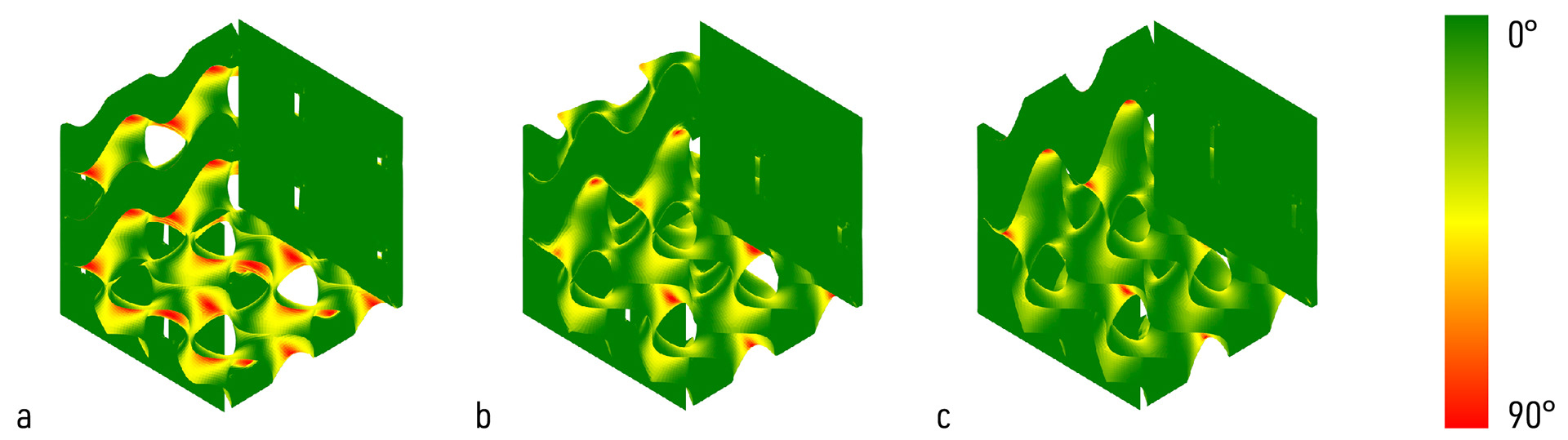
figure_04: draft angle analysis for several ovtests
Finally, one of the overhang samples was prepared for a series of compression tests, which demonstrated that the 3DPC gyroid structure could support over 1000 kilonewtons. Though large variability was observed in the performance of three gyroid samples tested, the research demonstrates that steep overhangs can be printed in concrete for gyroid-based structures.
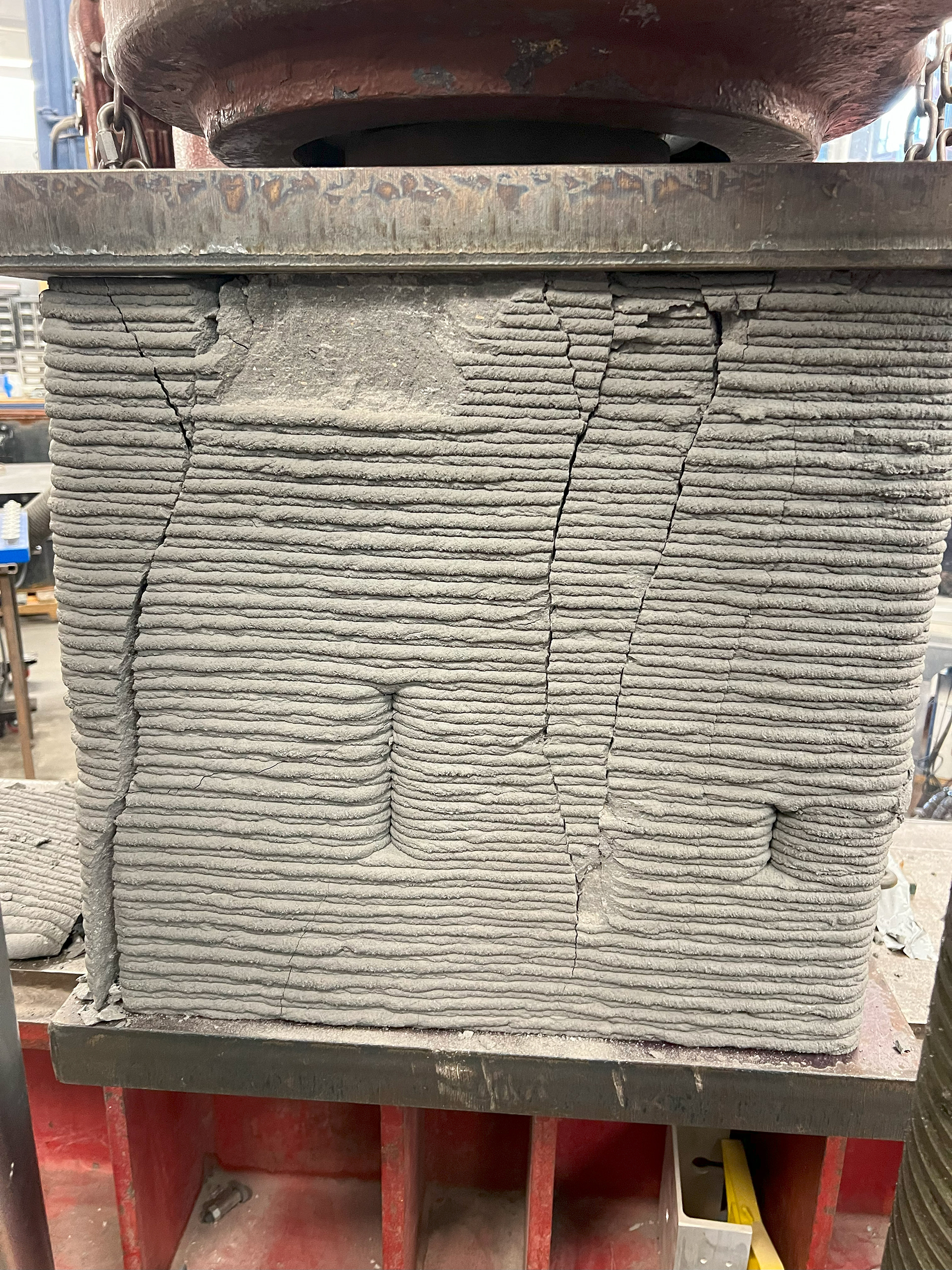
figure_05: compression test of gyroid sample